
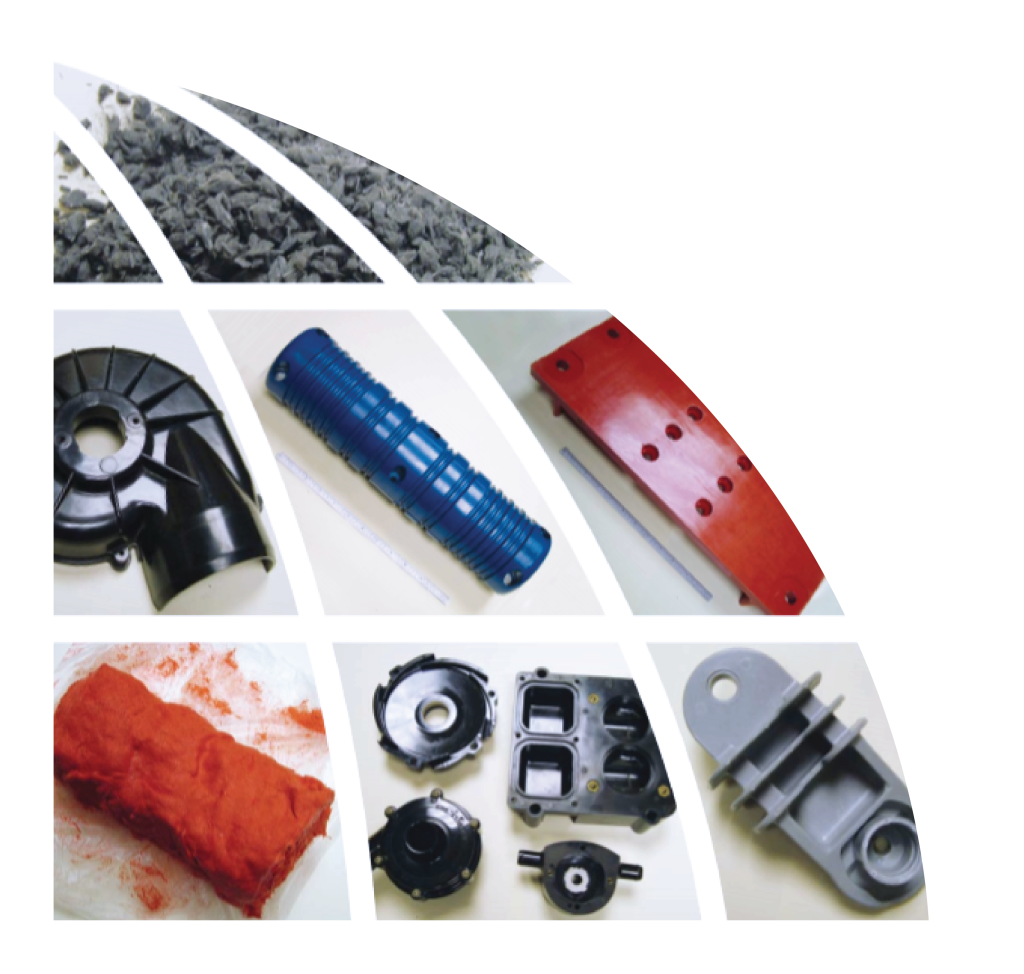
Welcome to Scott Molders, Inc.
Scott Molders, Inc. (SMI) is an industry leader in injection, compression and transfer molding of thermoset plastics. SMI provides quality products at an affordable price with a focus on continuous improvement and customer service.
Our Specialties
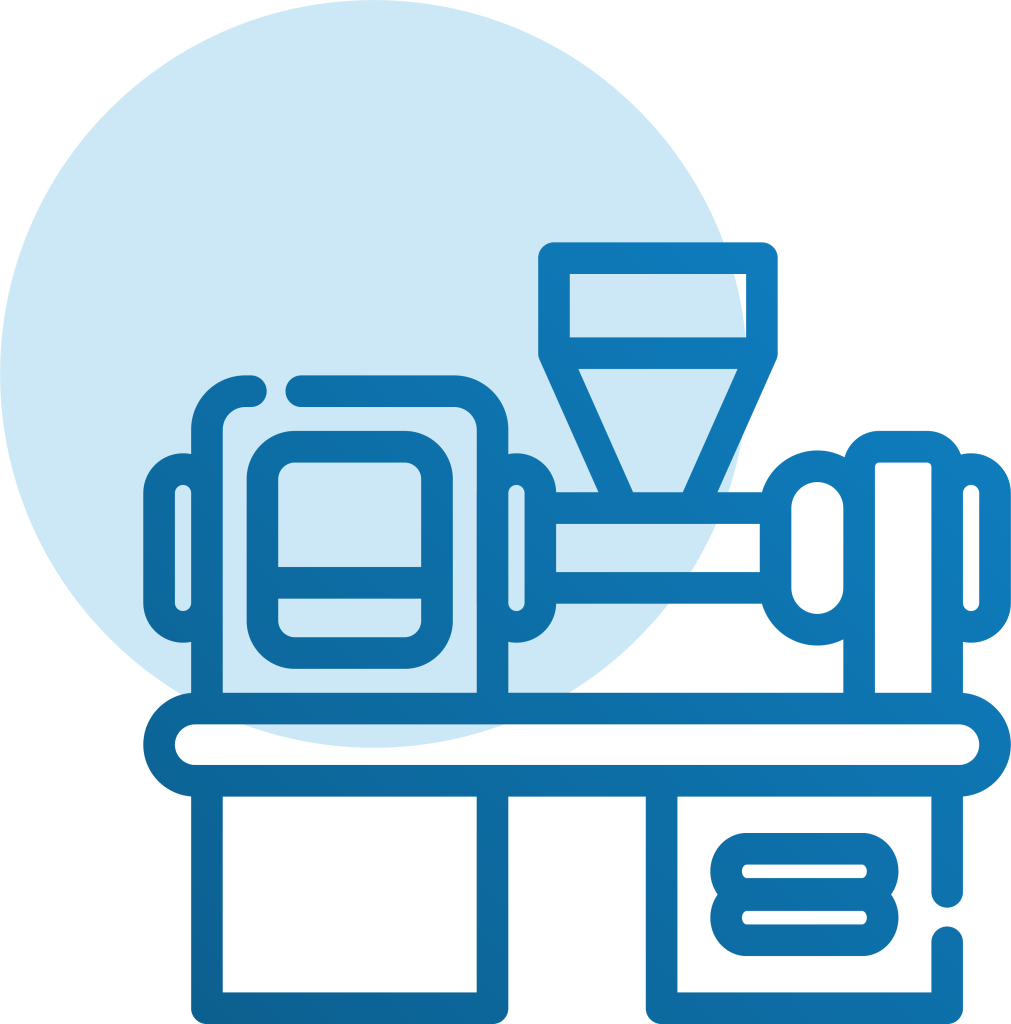
Molding
We have extensive experience creating molds using a variety of synthetic resins. Along with basic molding, SMI specializes in the design and molding of parts with molded in inserts and post molded pressed in inserts.
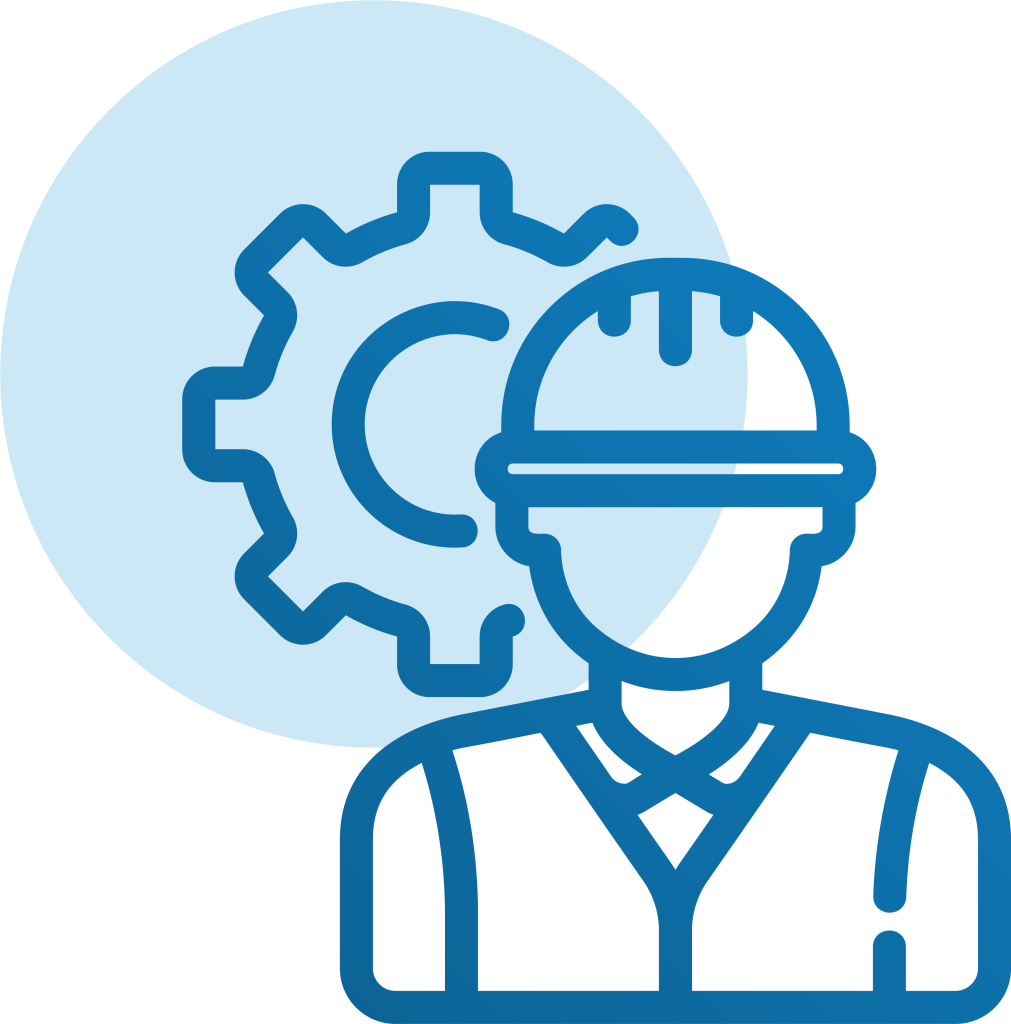
Engineering
Our engineering department utilizes modern designs and 3D software, assuring accurate conversion of your part files to tooling files, and to enhance our communication with both our customers and vendors.
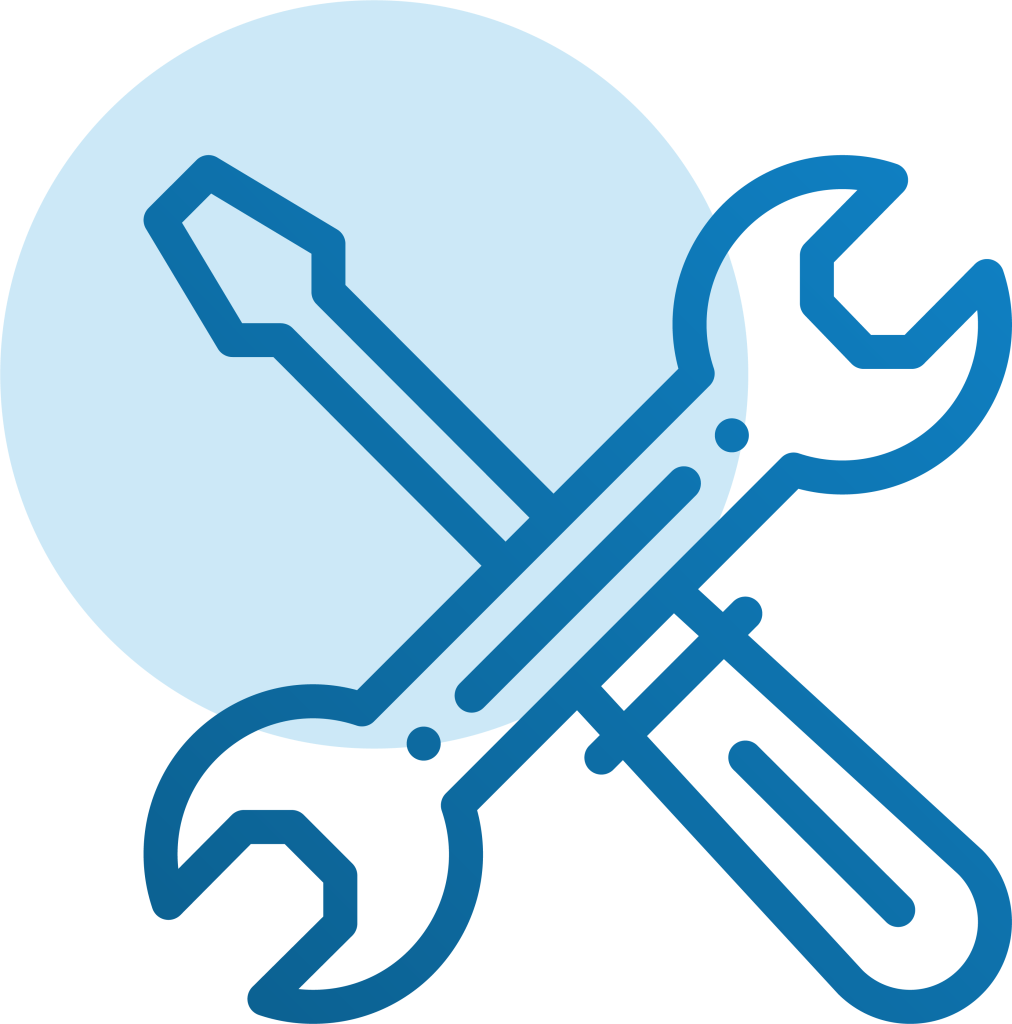
Mold Maintenance
Our main concentration is preventative mold maintenance (PM) and periodic mold assessments. Every mold, whether new or inherited, receives an initial, thorough, assessment.
Why Choose Us
We encourage early project involvement and can assist you in taking your product from inception to production.
In addition to our many different molding techniques and capabilities, we have secondary operation capabilities such as baking, drilling, tapping, machining, and light painting. Our quality department is self certified to many of our customers. Monitoring process and dimensional stability is our priority, thus ensuring the highest standard of part quality.
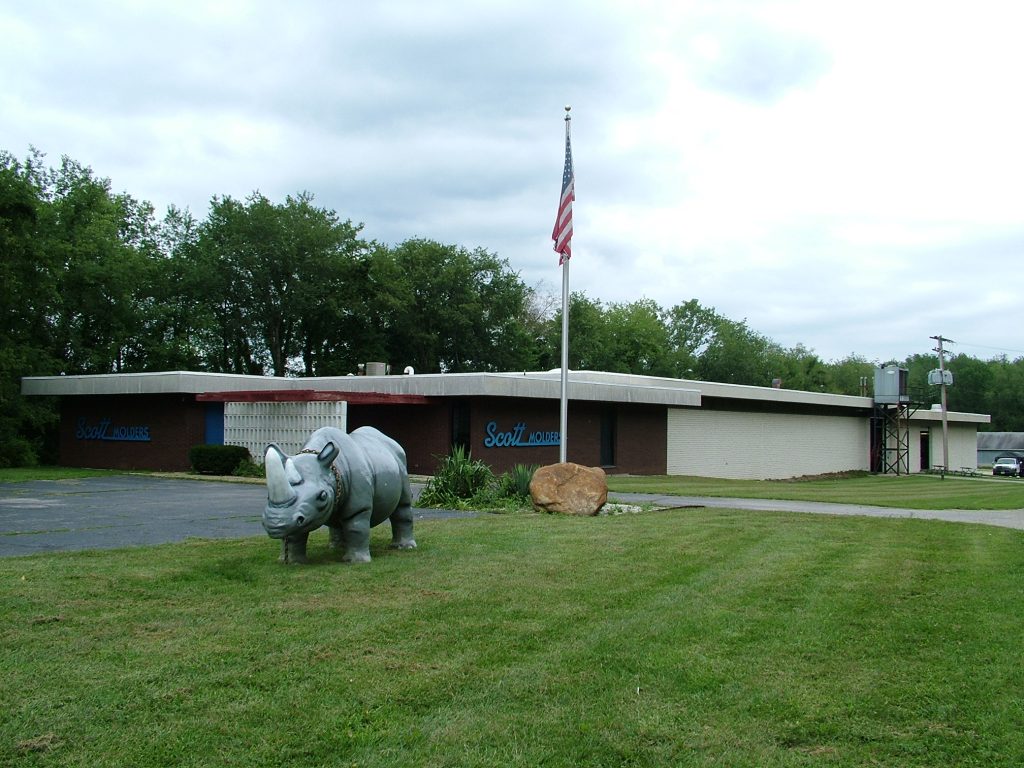
Molding
We have extensive experience creating molds using a variety of synthetic resins. Along with basic molding, SMI specializes in the design and molding of parts with molded in inserts and post molded pressed in inserts.
OUR SPECIALTIES
Basic Molding
We have extensive experience with phenolics, melamine-phenolics, urea’s, alkyds, DAPs and polyesters.
- These materials are processed utilizing injection, compression and transfer molding techniques.
- Our presses range from 50 tons to 400 tons. Many of our injection presses are equipped to process both granular and BMC materials.
Molded Inserts
We specialize in the design and molding of parts with molded in inserts and post molded pressed in inserts.
- Many different insert designs and materials are commonly used including brass, aluminum, steel, stainless steel, copper & beryllium copper.
- Passivating and chrome plating of inserts are commonly outsourced to many of our longtime partners of SMI.
OUR EXPERIENCE
Over the years, we have made it a point to build strong relationships with our vendors to mutually benefit all parties involved, especially you, our customer.
Additionally, the staff at SMI has a strong background in quality, mold design and engineering. Our well-rounded customer base has given us the experience and capabilities necessary to service the automotive, electrical, pump, aerospace, and utility industries.
OUR CUSTOMERS
We are an approved supplier to many renowned companies such as; Hubbell, Eaton, Siemens, Pentair, Safran, Wabtec, and Honeywell.
We are very confident that SMI can become your next valued supplier of thermoset molded parts.
Engineering
Our engineering department utilizes modern designs and 3D software, assuring accurate conversion of your part files to tooling files, and to enhance our communication with both our customers and vendors.
Whereas we have our own in-house mold design capabilities, we are also fortunate to have several vendors with which we have enjoyed much success in premier and innovative mold designs.
Our department’s average years of experience is approximately 30 years, thus affording our customers the level of comfort necessary in today’s competitive world. We can accommodate your budget utilizing either foreign or domestic mold builders.
Mold Maintenance
Our main concentration is preventative mold maintenance (PM) and periodic mold assessments (although we are capable of light repairs and polishing).
Every mold, whether new or inherited, receives an initial, thorough, assessment. After production is launched, preventative maintenance schedules are made. Accurate PM records are kept for the customer’s review. We strive for exceptional PM on our molds which helps in reducing downtime, repair costs and loss of molding efficiency.
Quality Assurance
Our quality system is designed to ensure that supplies and services provided by us and our vendors are subject to a thorough control of quality.
We utilize statistical methods that are beneficial in the control of our molding processes. We strive for early detection of discrepancies, so adjustments/corrections can be made in a timely manner, thus reducing scrap, improving efficiency, and, maintaining cost effectiveness. If, and when, problems arise, it is our priority to investigate, correct and prevent future occurrences. Continuous quality improvement is our top priority.
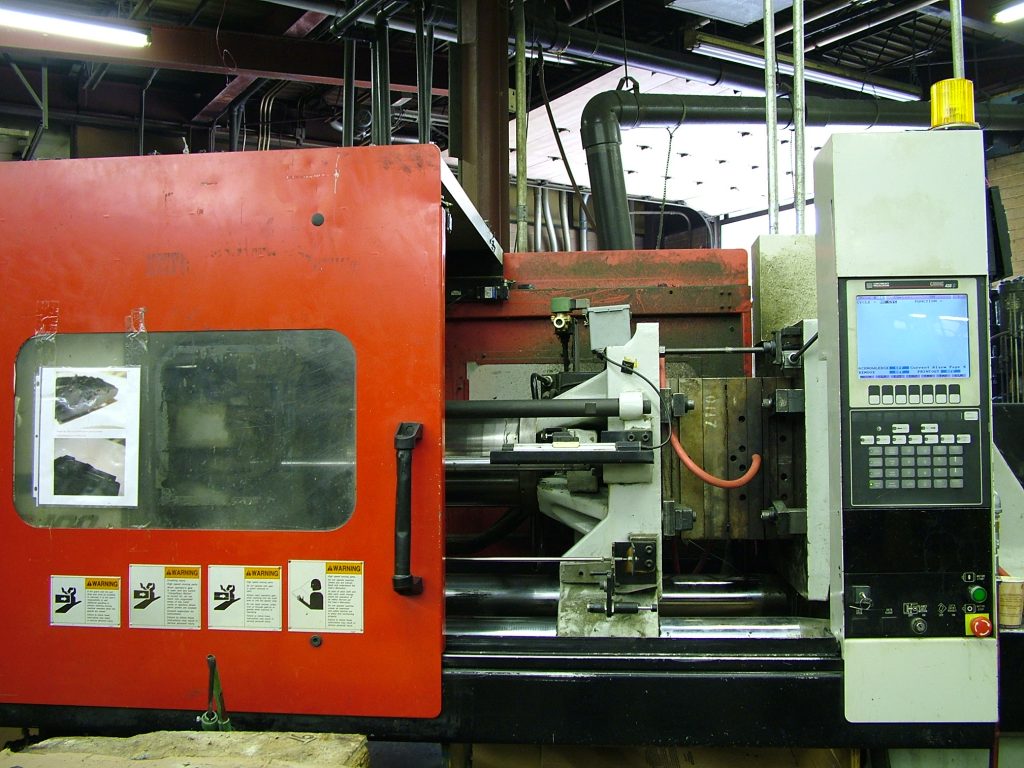
Our Facility
We operate out of a modern 26,000 sq. ft. manufacturing plant and a 6,000 sq. ft. warehouse that is situated on 5 acres. We employ ~50 people that work 3 shifts/5 days per week.
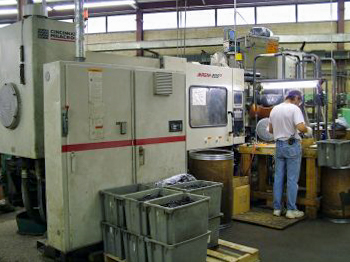
LOCATION
We are conveniently located within 6 miles of Interstates 80 and 76 and just a short drive to the major local airports.
- Cleveland Hopkins Airport – 35 miles
- Akron-Canton Airport – 22 miles
- Kent State Airport – 5 miles
EQUIPMENT
To create our molds, we utilize a variety of injection machines, compression/transfer machines, and preform machines, all with electronic preheaters and auxiliary power units to support them. We also have finishing equipment, blast cabinets, ovens, and drilling and tapping machines.
Check out our full equipment list.
- 12 injection machines ranging from 75 to 400 tons (many with oversized platens and stuffer capabilities).
- 22 compression/transfer machines ranging from 50 to 350 tons.
- 4 preform machines, up to 80 tons.
- Electronic preheaters, auxiliary power units, etc…to support the above.
- Finishing equipment: Pangborn, Wheelabrator, Jet Wheelblast and Isper deflashers, all connected to a central dust collection system within our blasting dept.
- 2 portable blast cabinets.
- 3 ovens for post baking.
- Drilling and tapping machines, including multi-head tappers and indexing tables (high speed air drill and tappers).
- Central vacuum system to assist in molding.
- 2 trucks.
- Flex/tensile test equipment.
- Well-equipped quality control department.
About Us
Scott Molders, Inc. was established in 1954 by Jack Yahner. An engineering manager at a local tool shop at the time, Mr. Yahner realized the opportunity for a new, modern molder of thermoset plastics.
Over the next several years, and while still managing the tool shop, he transformed the fledgling company into a molder worthy of such customers as Essex Wire, Bendix, Fisher Body, Westinghouse and G.E (just to name a few). Shortly after this accomplishment, Mr. Yahner began to devote his full attention to his company.
After changing locations several times to accommodate a growing company, he built the current plant in 1969 and it has since seen three expansions. The second and third generations carry on his innovative techniques and ideas today.
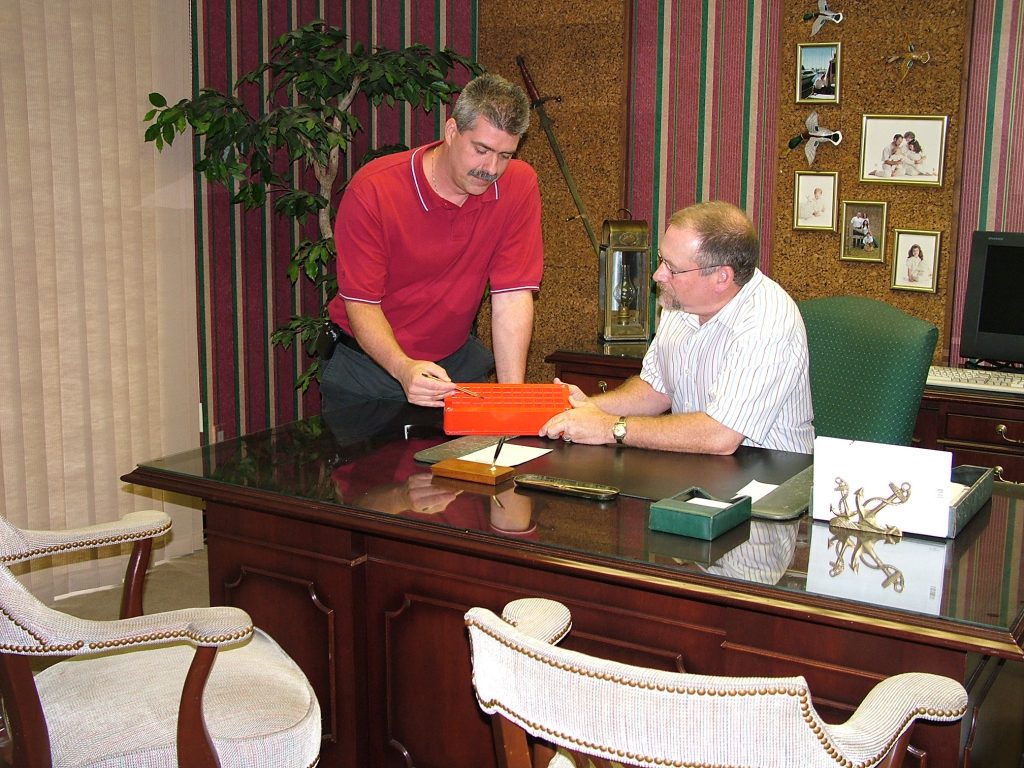
Contact Us
We welcome your inquiries for thermoset molded parts and invite you to visit our facility.
Scott T. Yahner
President
Glenn Russell
Vice President
Rob Robenstine
Plant Superintendent
Alex Yahner
Production Manager